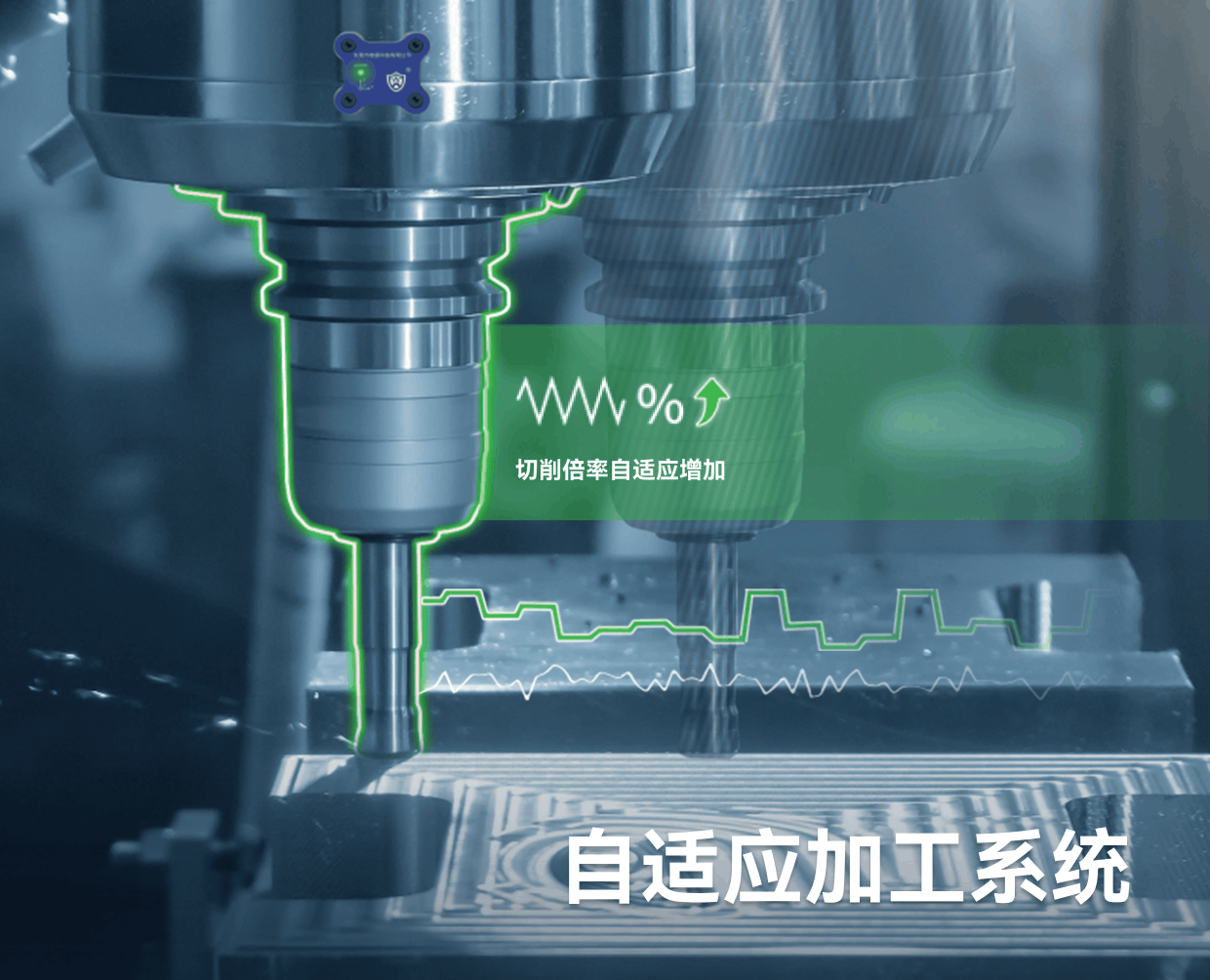
自适应加工系统
系统概述
华刃智造自适应加工系统是一款先进的智能制造解决方案,能够根据实时切削状态自动调整加工参数,优化加工过程,提高加工精度和效率,同时延长刀具寿命,降低生产成本。
系统通过集成的传感技术和人工智能算法,实时监测切削力、振动、温度等多种加工参数,智能分析加工状态,动态调整进给速度、主轴转速等参数,实现加工过程的自动优化。
核心优势
- 实时自适应:毫秒级响应,智能调整加工参数
- 多参数优化:综合考虑加工效率、质量和成本
- 自学习能力:持续积累数据优化加工策略
- 通用性强:适用于多种材料和加工工艺
技术原理
多源数据采集
系统通过高精度传感器网络实时采集切削力、振动、声音、温度、电流等多维数据,全面感知加工过程的各个方面。
智能分析与决策
基于深度学习和专家知识库的混合智能系统,对加工状态进行实时分析,识别当前切削条件下的最优加工参数。
闭环控制与反馈
系统与机床控制系统深度集成,根据分析结果自动调整进给速度、主轴转速等参数,形成闭环控制,持续优化加工过程。
自适应加工系统工作流程示意图
应用场景
复杂零件加工
适用于航空航天、模具等复杂形状零件加工,智能调整参数确保加工质量。
高精度零件制造
适用于精密仪器、医疗器械等高精度零件制造,保证尺寸精度和表面质量。
难加工材料切削
适用于钛合金、高温合金等难加工材料,优化切削参数,提高加工效率。
大批量生产
适用于汽车零部件等大批量生产场景,自动优化参数提高生产效率,降低成本。
系统效益
提高加工效率
通过智能参数优化,平均加工效率提升20%-40%,大幅缩短生产周期。
延长刀具寿命
智能调控切削负荷,延长刀具使用寿命30%-50%,显著降低刀具成本。
提升加工质量
实时调整避免过切或欠切,产品表面质量和尺寸精度提高15%以上。
降低生产成本
综合优化能耗、材料和刀具使用,整体生产成本降低15%-25%。
客户案例
某汽车零部件制造企业
该企业引入华刃智造自适应加工系统后,在变速箱壳体加工生产线上实现了以下成果:
- 生产效率提升35%,年产能增加2万件
- 刀具成本降低42%,每年节省刀具支出约60万元
- 产品合格率从96.3%提高到99.7%,大幅减少不良品
- 设备能耗降低18%,符合绿色制造要求
"华刃智造的自适应加工系统帮助我们在保证质量的前提下显著提高了生产效率,是我们数字化转型的重要一步。"
— 客户生产技术负责人